We’re more than happy to announce our latest partnership with Glenn Nichols, restoration maestro and electric guitar experimenteur. The curves of his Corralitos model are velvet smooth in hand-rubbed varnish and a dark burst, with McNelly Bliss humbuckers and adjustable bridge (more on that later), and it’ll be available on our site soon. In the meantime, we chatted with Glenn about how his journey into lutherie and all the ways he’s pushing the envelope with his Corralitos model, from varnish finishes and Cedar necks to vacuum pressing the top laminates and implementing a wedge-adjustable saddle. Once we unpacked his guitar and tuned it up, the immediate response was, “Woah.” And it continues to wow us, even now. Enjoy our conversation with Glenn below, and look out for that Corralitos soon!
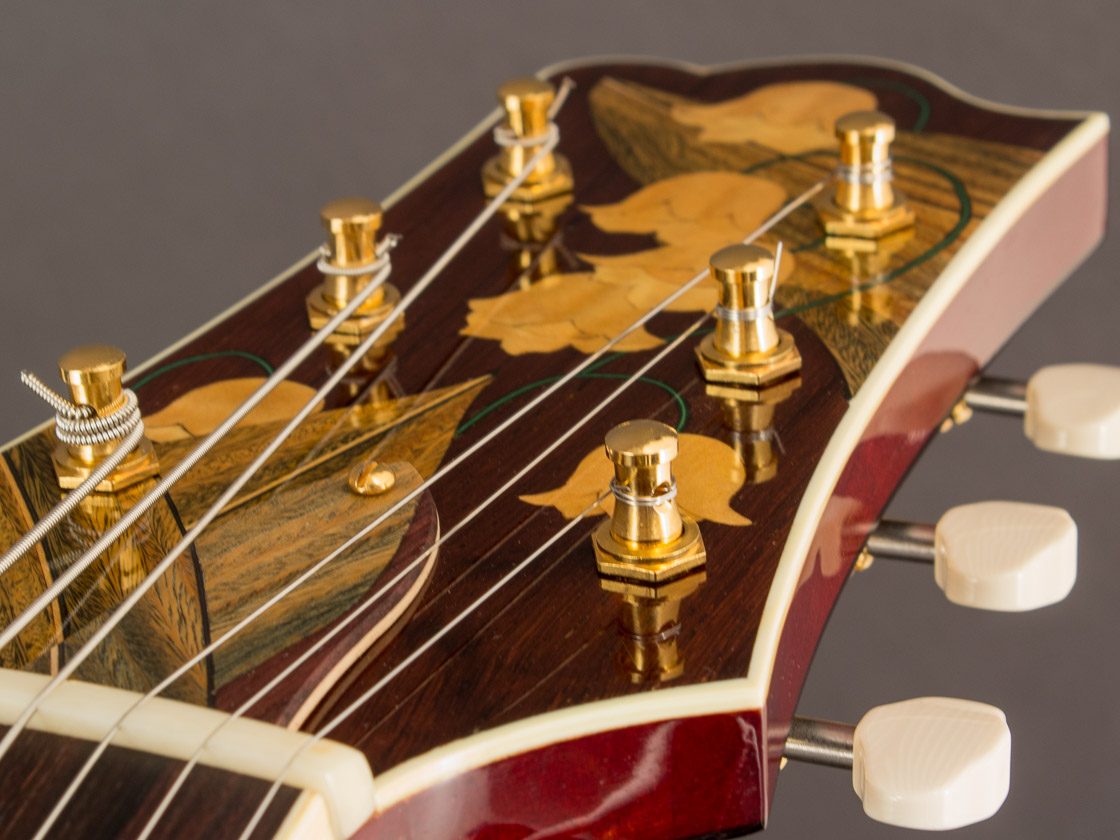
LW: You’ve been in the repair business for some time. What came first, fixing guitars or building them.
GN: My journey into restorations is the opposite of most repair people. I started at the end and worked my way backwards. My first job in the industry was in the finish department at Santa Cruz Guitar Company. I attended the Roberto-Venn School of Luthiery in 2003, which resulted in an entry level position spraying lacquer for SCGC. As my skills developed, I found myself running the finish department. This ultimately made every ding, scratch, or crack that happened in production my responsibility to fix. When you are repairing an old guitar there is some acceptance that the damage may show. When you are repairing a new guitar, it has to be perfect, or it’s no longer a new guitar. By the time I started to do restorations and structural repairs on my own, it all made sense to me. My time spent at Santa Cruz gave me the confidence to take on high-end and vintage work. I knew that in the end the repair would look good, because that’s what I had been doing for years.
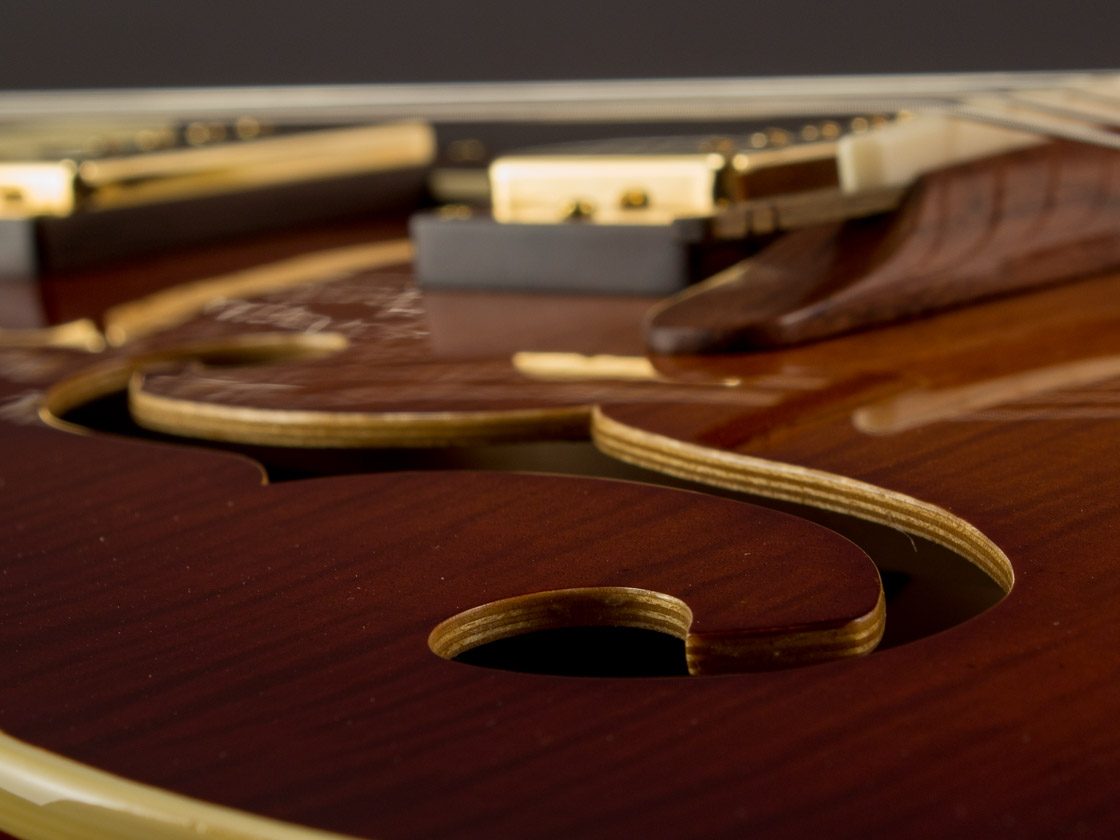
LW: Your finish work is particularly impressive. Have you always gravitated towards finish work, or did you just wake up one day surrounded by air brushes and cans of lacquer?
GN: Ha ha! I have been a visual artist for as long as I can remember. I received a Bachelor degree in Fine Art from The Montserrat College of Art in 2002. I guess I traded in my paint brushes and tubes of paint for air brushes and cans of lacquer. Lots of builders come from a woodworking or engineering background, and when it comes time for finish the struggle begins. This is why so many builders farm out their finish. I’m not making judgements, it’s just that the learning curve is tremendous! After I spent nine years at SCGC learning nitro, I went to work for Kenny Hill Guitars to learn French Polish. This opened up a whole new world of materials and processes. I experimented with all sorts of shellacs, resins, oils, and alcohols. I started to mix my own varnishes. Again, by starting from the end and knowing the results that I wanted, it was easier for me to manipulate the materials. You won’t find lacquer on my guitars. The neck is a spirit varnish, taken from the European classical tradition. In my opinion, it just feels right, a hand-rubbed finish in your hand. The body is an oil varnish, taken from the marine industry. This varnish was originally used on Spruce masts, very durable and tough, but allowing for movement and vibration. My finish choices are not afterthoughts. The guitar is constructed as a canvas for these different finishes.
LW: I’ve seen an adjustable bridge & saddle setup like the one on your Corralitos model before, but I’m curious about its origins, and how you came to use it.
GN: I first saw this style of bridge on one of Christian Mirabella’s archtops. I had developed a similar, two-piece bridge that was not adjustable. The saddle had to be sanded to drop the action, just like an acoustic saddle. A traditional archtop bridge floats on two adjustable posts between the bridge and the saddle. This method has been used forever on great-sounding guitars, but I wanted a solid connection to the top. Everything that I had learned in the flattop and classical world depended on tone transfer at the bridge. Once I saw the wedge bridge, it all clicked into place. I may be able to have my cake and eat it too. Before I began, I emailed Chris Mirabella out of respect and asked for his blessing in exploring the design. A true gentleman, he promptly returned my email, offered his help and support, and told me the history as he knew it. Chris got the design from one of his close friends and mentors, Jimmy D’Aquisto, who had taken inspiration from a German upright bass maker. It was very important for me to have permission, and to do what I thought was the right thing. There is a lot of borrowing and appropriating in guitar building. I’ve found that in my generation of builders, we are very open and willing to share, as long as it is done honestly.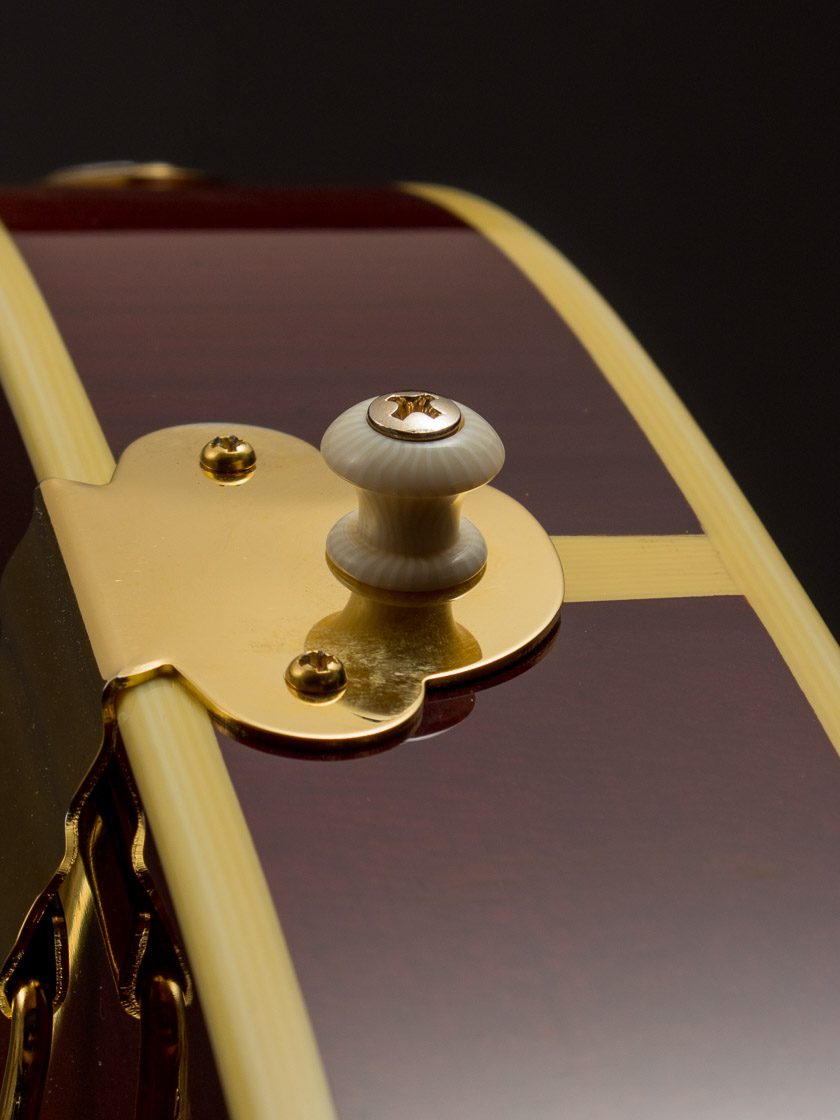
LW: What do you enjoy doing outside of building instruments?
GN: I am married and have two daughters, so they keep me busy. My new shop is in my home, so my family is a huge part of my life. I also have to admit that I’m a bit obsessed with Brazilian Jiu Jitsu. It was something that I picked up in Santa Cruz to relieve stress. I think most artists and musicians can be a little obsessive compulsive. It’s important to have a healthy outlet.
LW: I understand that you now share a shop with one of our favorite luthiers, Bill Tippin. What’s it like to work along side Bill?
GN: Bill is a long time friend and I think we have a very special relationship. I spend a couple of days every week working in Bill’s shop, doing whatever is on the agenda for the day. Bill is first and foremost a craftsman, and his shop is set up as such. He doesn’t have an assembly line, or a strict list of processes that are never to be broken. He is open, and creative, and willing to take chances. That’s why his guitars are so special. He allows for growth and progression. Bill could build you a guitar, a table, a fishing rod, or a boat. And they would all be top notch! We drink coffee, listen to blues, and solve problems. We laugh, and cuss, and work on guitars. Bill pushes me to do the best work that I can. Sometimes, he pushes me past what I think can be done, just to see if I can do it. I am very fortunate to have him as a mentor, and it all runs pretty smoothly, as long as I put his tools back where I found them.
LW: What music are you listening to right now?
GN: The Marcus King Band, I think they may be from your neck of the woods. Great guitar playing, solid band. I always have blues playing in the shop. I’ve been on a Hound Dog Taylor kick this week. I’ve been teaching my daughters how to play slide guitar. My seven year old plays a killer slide version of Beat on the Brat by The Ramones.
LW: What’s the most interesting repair or restoration job you’ve ever worked on?
I’m really lucky to have a lot of boutique and vintage instruments cross my bench. Sometimes the expensive ones are just guitars, and the cheap ones will put a smile on your face and leave you scratching your head. Sometimes a guitar will live up to its reputation and you may have to stick a mirror in the soundhole and figure out where the magic is coming from. I had a couple of laminate top restorations come through my shop that changed my life. They were an old Gibson ES- 225, and a Martin GT-70. They both really struck a chord with me, and when a guitar builder gets Guitar Acquisition Syndrome it can be a problem. Being in my line of work, I couldn’t afford to buy one, so of course I decided to build one. I started building the jigs and fixtures in a small shed in my backyard in Corralitos, CA. Those funky old laminate guitars were my inspiration for the Corralitos model.
LW: Lastly, can you speak to what kind of play feel and voice you’re shooting for with your Corralitos? What sets it apart
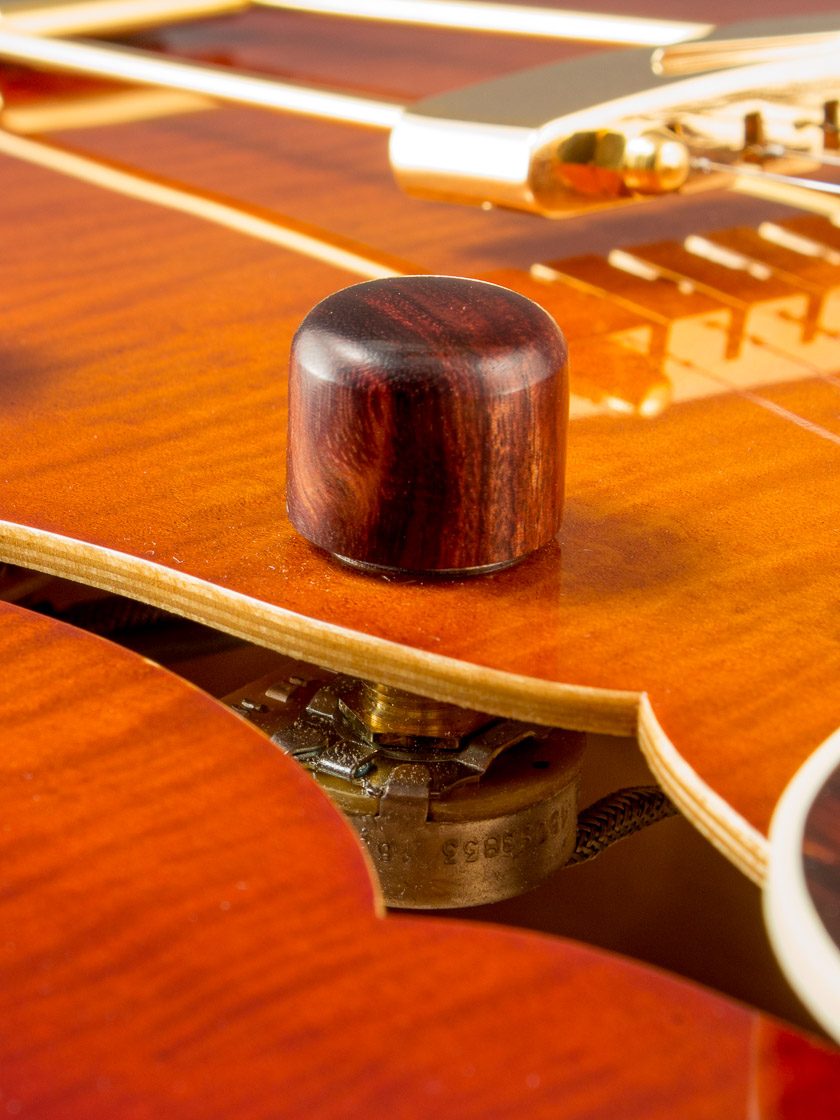
from the pack?
GN: My goal with the Corralitos is to bring boutique methods of building to what is historically a factory guitar. The old laminate tops of the 50s and 60s were stamped out with large hydraulic presses, using three or four sheets of Maple or Birch. While they sound good amplified, acoustically they can be dead, flubby, and sometimes tinny and thin. The general rule with electric guitars is, if it sounds great unplugged, it will sound great amplified. I use six thin, alternating layers of Maple and a vacuum press to form each layer, plate by plate. The result is a very light, yet stiff top. Traditionally, top woods are chosen for their strength-to-weight ratios. The use of a vacuum press insures that there are no voids between the plates. The wood is not crushed into shape, it is pressed in an air tight chamber. (I have written a blog on my website that goes into greater detail of the laminate top process) [you can find that blog here: http://glenn-nichols-guitars.com/]. Attention to the details of the plate construction and bracing can produce a top that is very lively and responsive when played acoustically, while the alternating laminates help to reduce feedback when played at high volumes. The use of a varnish, rather than a lacquer, helps to add a beautiful warmth to the tone. I believe that the varnish makes the guitar feel more broken in than a brighter-sounding lacquer finish.
Another difference that doesn’t stand out unless you pick it up, is the overall weight. This particular guitar weighs in at 5.4 lbs , which is very light for an electric guitar. I used Spanish Cedar for the neck, blocks, and kerfings. While Spanish Cedar is a staple in classical guitars, it is not often used on electrics. I perform a lot of French Polish restorations on classical guitars and I believe that a French Polished Spanish Cedar neck is the perfect feel for any style of player. The use of Cedar not only cuts down on weight, paired with the varnish and French Polish, it also smells wonderful.
The pickups are handmade McNelly Bliss humbuckers. They are a low output pickup, based on old PAFs, but with a little more presence. They are very sensitive, and the clarity vs breakup can be easily dialed in by raising or lowering the pickup to taste. I used a 1950s style wiring with paper in oil caps to bring the full vintage vibe to life. I designed this guitar to be able to handle sweet and clear acoustic tones, to jazz comping and soloing, to overdriven blues and rock.
Excited to see this Corralitos for yourself? It won’t be long! Coming soon to a Dream near you.